Insights into Building Materials Manufacturing in India
Cement is the foundation of modern construction. It serves as the primary building block for infrastructure projects. Cement manufacturers play a critical role in transforming raw materials into cement. In this article, we'll explore how cement manufacturers in India create this essential building material.
Cement production involves multiple stages, each requiring specialized machinery and expertise. Let's dive into these stages to understand how building materials manufacturers in India produce high-quality cement.
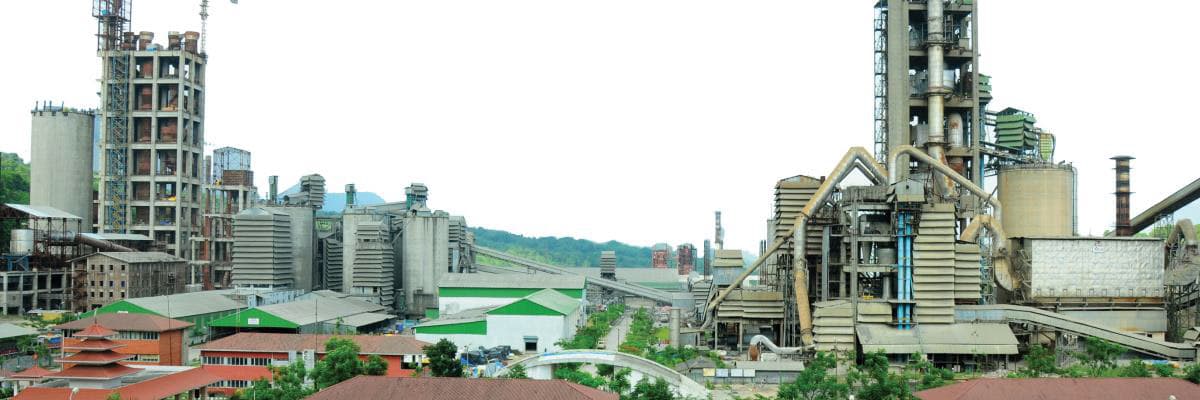
Interested in learning more about Star Cement's products? Visit our website to discover our range of cement and building materials.
Cement Manufacturing Process: From Quarry to Kiln
Raw Material Extraction
The process begins with the extraction of raw materials. Limestone and clay are the primary materials used in cement production. Cement manufacturers in India source these materials from quarries. The quarries must be strategically located to ensure a steady supply.
For example, Star Cement operates quarries in areas with abundant limestone deposits. These quarries are crucial to maintaining a consistent flow of raw materials to the cement plant.
Crushing and Grinding
Once extracted, the raw materials undergo crushing and grinding. This step involves breaking down large rocks into smaller pieces. Cement manufacturers use jaw crushers and cone crushers to accomplish this. The goal is to create a uniform size for the raw materials.
After crushing, the raw materials go through grinding. Grinding turns the materials into a fine powder, known as raw meal. This step is essential for the subsequent stages of cement production. Building materials manufacturers in India invest heavily in grinding technology to ensure quality and consistency.
Raw Mix Preparation
The raw meal must have a precise chemical composition. Cement manufacturers mix it with additives to achieve the desired properties. The exact composition depends on the type of cement being produced. For instance, adding iron ore or bauxite can create a specific cement type.
Star Cement, a leading cement manufacturer in India, prioritizes quality control at this stage. They perform rigorous testing to ensure the raw mix meets the required standards. This level of precision contributes to the quality of the final cement product.
Clinker Production
The raw mix then enters the clinker production stage. This is where the kiln comes into play. The kiln heats the raw meal to extremely high temperatures. The intense heat triggers chemical reactions, leading to the formation of clinker. Clinker consists of small, gray nodules that are the key component of cement.
Cement manufacturers use rotary kilns for this process. The kiln's rotation ensures even heat distribution. The high temperature, often exceeding 1,400 degrees Celsius, drives the chemical changes required for clinker production.
The Role of Kilns in Cement Production
The kiln stage is central to cement manufacturing. It involves calcination, where carbon dioxide is removed from the limestone, creating calcium oxide. This reaction is critical to the formation of clinker. The kiln's continuous rotation ensures thorough processing.
Star Cement uses advanced rotary kilns designed for efficiency and sustainability. They also focus on environmental responsibility, using alternative fuels and energy-efficient systems. These measures help reduce emissions and align with India's sustainability goals.
Cement Grinding and Packing
After the clinker cools, it undergoes grinding to become cement. Cement manufacturers in India use ball mills or vertical roller mills for this stage. The grinding process produces a fine powder, the final cement product used in construction projects.
During grinding, cement manufacturers add gypsum to control the cement's setting time. Gypsum ensures that the cement hardens at a consistent rate, crucial for construction applications. After grinding, the cement is either packed in bags or stored in bulk.
Star Cement offers a range of packaging options to suit different customer needs. This flexibility is why they are trusted by many building materials manufacturers in India.
Discover more about Star Cement's grinding and packing process. Learn how we ensure the quality and consistency of our products.
The Role of Cement in India's Infrastructure
Cement is fundamental to India's infrastructure development. It's used in constructing roads, bridges, buildings, and other essential structures. Cement manufacturers in India play a vital role in supporting these projects.
Star Cement's Contribution to India's Infrastructure
Star Cement, one of India's leading cement manufacturers, plays a significant role in supporting the country's infrastructure development. The company's commitment to quality and innovation has made us a trusted partner in major construction projects across India.
Star Cement's products have been used in a variety of infrastructure projects, including:
- Highways and Roads: Star Cement's high-quality cement has contributed to the construction of national highways, offering durability and resilience to India's busy road network.
- Airports: The company's cement is used in the construction of airport runways and other critical airport infrastructure, ensuring safety and reliability for air travel.
- Urban Developments: Star Cement supports the growth of India's cities by providing cement for residential and commercial construction projects. This contributes to the expansion of smart cities and urban development initiatives.
- Bridges and Dams: Star Cement's products have also been used in the construction of bridges and dams, highlighting the company's versatility and commitment to quality.
By providing high-quality cement and building materials, Star Cement contributes to India's growth and development. Our dedication to innovation and sustainability ensures that our products meet the demands of modern infrastructure projects.
Conclusion
Cement manufacturing is a complex process with multiple stages. It requires careful planning, advanced technology, and strict quality control. Cement manufacturers in India, like Star Cement, produce high-quality cement that supports the country's infrastructure needs.
The future of India's infrastructure relies on high-quality building materials. Cement manufacturers will continue to play a critical role in supporting the nation's growth, providing the foundation for a wide range of construction projects. With a focus on sustainability and innovation, India's cement industry is poised to meet the challenges of tomorrow's infrastructure needs.
If you're looking for premium cement or building materials, consider Star Cement. We offer a wide range of products to meet your construction requirements.
Visit Star Cement's website here to explore our products and learn more about our sustainability initiatives. You can also find information on our services and support for construction projects.